Table of Contents
ANCIENT ART OF JAIPUR BLOCK PRINTING
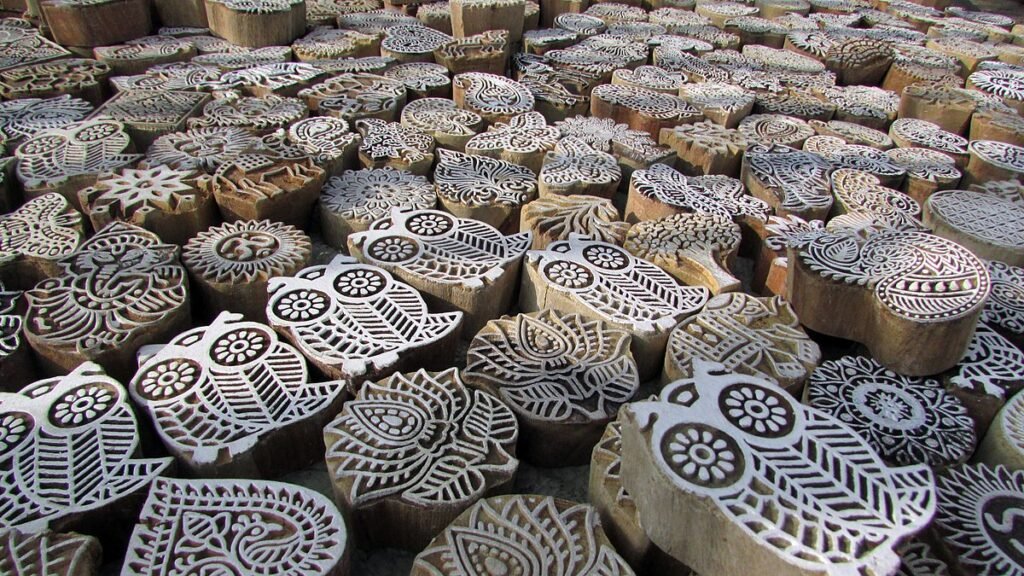
What is Hand Block Printing?
Hand block printing is a traditional art of printing fabric using wooden block as a medium on which designs carved on it and dipped in color dyes and printed on fabrics. This art which is more than 500 years old is still prevalent in Jaipur Rajasthan. Its commonly used to bring our lively traditional and modern design to life on home décor products like curtains, bedsheets, and quilts. With love for traditional style picking up again in a newer generation this art is also used on apparel both man and woman with modern design on them which ensures they are modern and still connected to old roots.
Process of Block Printing Involves the following:
- Wooden Blocks
- Color Dyes or Pigments
- Printing Process of fabrics
Wooden Blocks
Firstly, the design to be printed on fabric is drawn on tracing paper by hand. Then this tracing paper is placed on wooden blocks and artisans then carefully using a wooden hammer and chisel try to carve out the same design on the wooden block as on paper. It is an intricate process that involves from few hours to few days to carve design on the wooden block based on the complexity of the design. This art of making the design on the wooden block is done by few hundreds of artisans here in Jaipur who have inherited this art from their forefathers and they try to pass it out to the coming generation.
Any complex design is usually carved out on wooden blocks in a set of 3-4 wooden blocks. The number of blocks for a particular design depends on the colors present in the design and the complexity of the design.
Color Dyes
Colour dyes used for block printing usually are Vegetable dyes made from natural ingredients or AZO-free dyes. With the advent of awareness among consumers about the products, they consume use of vegetable or azo-free dyes have increased even though this increases production costs.
Vegetable Dyes
Vegetable dyes or Natural dyes are dyes or colorants derived from plants, invertebrates, or minerals. The majority of natural dyes are vegetable dyes from plant sources—roots, berries, bark, leaves, and wood—and other biological sources such as fungi. One of the most common natural dyes used in block printing is Indigo dye.
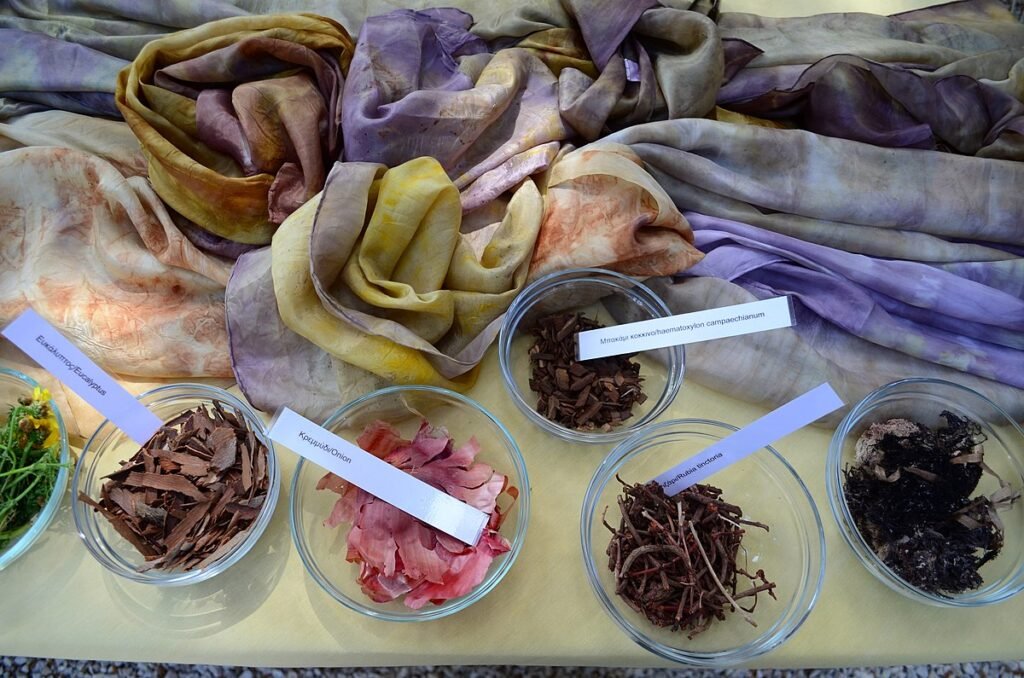
Indigo dye is an organic compound with a distinctive blue color. Historically, indigo was a natural dye extracted from the leaves of some plants of the Indigofera genus, in particular, Indigofera tinctoria; dye-bearing Indigofera plants were commonly grown and used throughout the world, in Asia in particular, as an important crop, with the production of indigo dyestuff economically important due to the previous rarity of some blue dyestuffs historically. Indio dye block prints are quite popular in bedsheets, quilts, and woman apparel. As it gives quite a unique look which quite resembles blue’s of jeans but still contain its original look.
AZO-Free Dyes
Azo-free dyes became quite popular also in block printing due to their cost-effective process. As producing natural dyes is a long tedious process and also expensive thus mass-produce synthetic dyes came in prevalence and with awareness and regulation AZO-free dyes were produced as earlier the AZO dyes contain carcinogenic material which was harmful to humans. Nowadays all commercial synthetic dyes used in block printing are AZO-free dyes ensuring they are not harmful to humans and neither leaves a hazardous footprint on the environment.
Printing Process: How Does Block Printing Process Take Place!
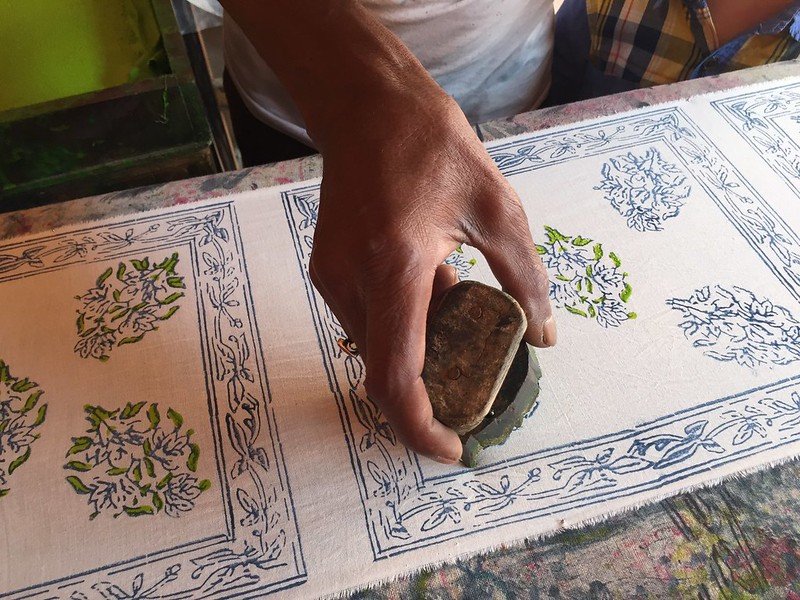
As by now, we have come to know the ingredients of the block printing process, now we will know how does all this combine to bring out beautiful designs on fabrics.
Step 1:
First of all, the fabric used for printing is RFD (Ready for Dyeing) this process involves soaking the fabric in hot water, bleaching, and then drying. RFD of fabric is done to remove wax, oils, darts, and sizing material applied before weaving to make the fabric ready for dyeing. Scouring is done to improve dye uptake and absorption into the fabric and improve evenness in dyeing throughout the fabric length.
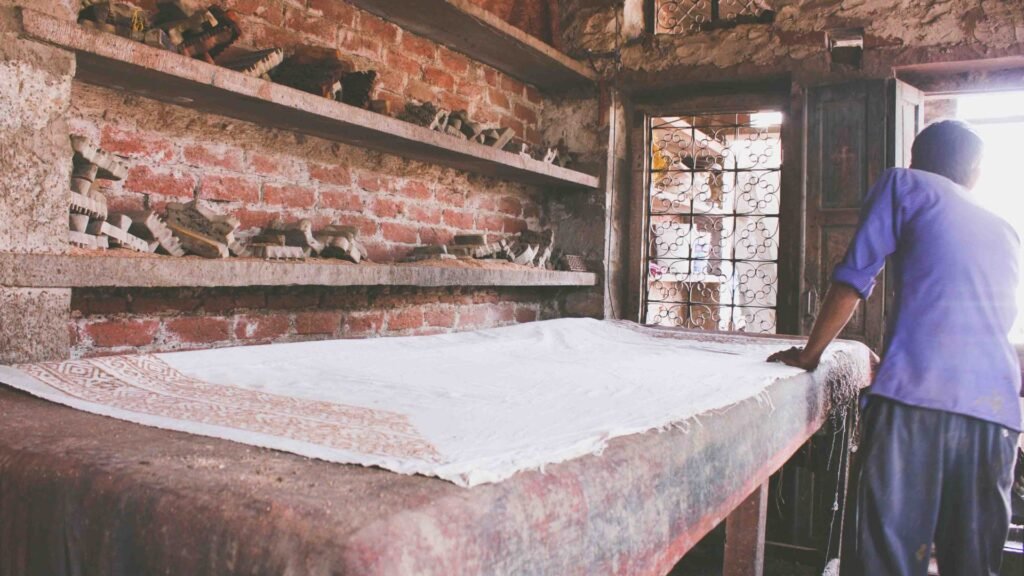
Once this is done the processed fabric is laid on long tables usually of length of over 20 feet’s evenly ensuring there are no wrinkles in the fabric. Ends of fabrics across the are fixed by pins which are placed on it piercing it and on a mat on the table to keep the cloth from moving while doing the printing
Step 2:
Secondly now the wooden blocks with design on them carved out which are selected are dipped in the natural or azo-free dyes placed in vessels/containers and are placed next to a table with a sliding trolley. These sliding trolleys are moved along the table for easy dipping and printing to continue. Dipped wooden blocks with colors are imprinted on the fabric in sequence. This means one color of the design is first printed on the fabric than the next and so on. Maintaining sequence in printing is the essential art of block printing because if you miss one step there is a high chance of the design being misrepresented. Due to these trained artisans only do it as one can do this by himself as a hobby but to bring a large number of uniform products with designs on them require experience and patience.
Step 3:
Lastly, once the design is printed in sequence on the fabric these fabrics are kept in natural sunlight to dry. This natural process of drying ensures that pigments of colors stick to molecules of fabric to wash long-lasting colors after wash. After drying these fabrics are ironed out and send to the final destination for either being stitched into apparel or weaved into quilts or bedspreads as per requirements of clients.
Conclusion: Future of Block Printing
As people are turning towards their roots back and trying to connect to their old heritage and relive the moment of its glory. This ancient art has again come into prevalence thanks to its large appearance in social media and mainstream fashion. Nowadays with a large number of entrepreneurs with help from artisans of this art can bring this printing style to mainstream medium. With easy internet access to showcase their products in many ways be it their website or social media platforms, they can connect to people in every nook n corner of this world.
As there is saying in old times art never dies it just transforms itself with changing times to different tastes n styles and able to live among us. Seeing this we are hopeful that JAIPUR BLOCK PRINTING art will live and strive to newer heights in the coming future.